« Voir toutes les perspectives
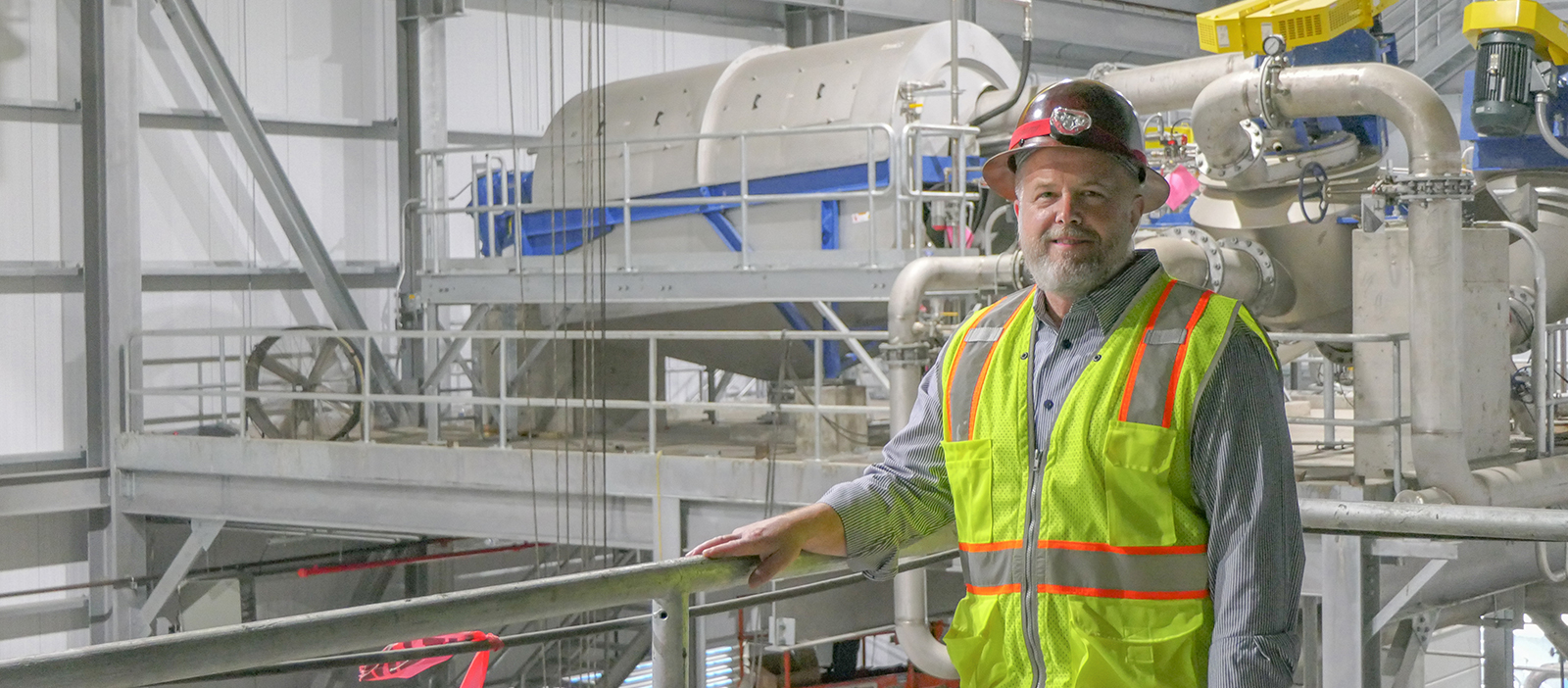
Kevin Haney ne peut pas s’éloigner du papier. C’est dans les fibres de son maquillage pour ainsi dire. Kevin, directeur régional de la fabrication de Sonoco pour la division du papier, a déménagé dans l'entreprise au cours de ses 30 ans d'ancienneté, occupant des postes dans les secteurs du papier, du recyclage et de l'exploitation, mais sa passion et son histoire avec le papier l'ont ramené à un poste de direction dans sa division d'origine. C’est un poste dans lequel Kevin prend énormément de responsabilité et de satisfaction alors que son père et son grand-père travaillaient tous deux dans des usines de papier. Il aime non seulement le travail quotidien, mais il est fier de l’héritage qu’il vit et laisse aux communautés.
De nos jours, l’une des principales responsabilités de Haney est de gérer Project Horizon, un projet visant à transformer la machine à carton ondulé moyen (machine no 10 ) de Sonoco à Hartsville, en Caroline du Sud, en une exploitation de carton recyclé non couché (URB) de pointe avec une capacité de production annuelle de 180 000 tonnes. La nouvelle machine a été conçue dans le but d’être le producteur d’URB le plus important et le moins coûteux au monde. Project Horizon is expected to be completed by the end of the second quarter of 2022.
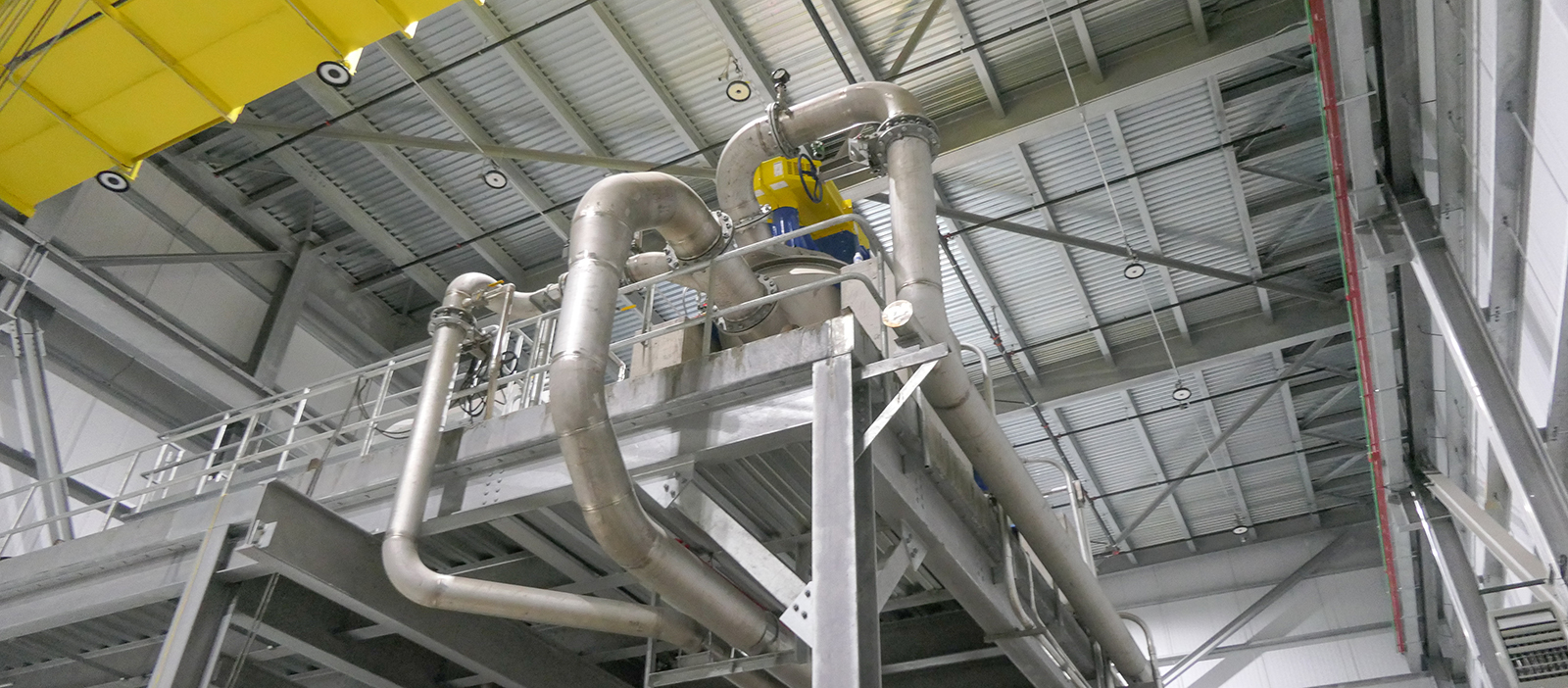
Nous avons parlé à Kevin pour en savoir plus sur son parcours Sonoco et sur la direction du projet Horizon.
Pouvez-vous nous parler un peu de vous et de votre histoire Sonoco?
C’est une histoire assez simple. Sonoco est la première et la seule entreprise pour laquelle j’ai travaillé depuis mon diplôme de la N.C. State University. Je travaille chez Sonoco depuis 30 ans, dont 28 au siège social de Hartsville, en Caroline du Sud. J'ai commencé à travailler dans la division du papier et j'ai gravi les échelons jusqu'à un poste de gestionnaire. À partir de là, je suis allé à la division du recyclage en tant que directeur régional, puis directeur des opérations, mais j’ai tellement manqué la division du papier que je suis revenu après quelques années. Aujourd’hui, en tant que directeur régional de la fabrication pour la division du papier, j’ai des responsabilités pour les opérations de Hartsville et de Richmond, en Virginie.
Vous faites partie de la gestion du projet Horizon. Pourriez-vous nous dire comment le projet s’est déroulé?
Le projet Horizon fait partie de notre système d’optimisation des actifs en Amérique du Nord et en est à la phase deux. La phase 1 impliquait des mises à niveau de nos usines de premier niveau, qui sont nos usines à moindre coût et plus rentables. Au moment de la première phase, notre président-directeur général, Howard Coker, était vice-président directeur de la division industrielle mondiale. Il est venu nous demander quelle serait la prochaine phase. Nous savions que la prochaine phase serait de traiter une opération vieillissante ici à Hartsville. Les coûts augmentaient et nous étudiions la possibilité de devoir arrêter certaines des machines plus anciennes et plus coûteuses. Si nous n’avions rien fait, nous devions probablement fermer le No. 10 ainsi que d’autres machines. La gestion du papier s’est réunie et nous avons eu quelques décisions à prendre.
Nous avons d’abord examiné ce projet pour reconstruire la machine no 10 à Hartsville en 2005 lorsque notre partenaire nous a informés des plans de ne pas renouveler le contrat de coentreprise. Personne n’était trop enthousiaste à l’idée d’avoir à dépenser ce genre d’argent à l’époque, alors lorsque Howard a demandé nos plans de phase deux, nous avons décidé qu’il était temps de convertir la machine no 10 en machine URB, ce que le reste de notre système d’usine fabrique. Cette conversion ferait de la machine no 10 le producteur d’URB le plus important et le moins coûteux au monde et assurerait l’avenir du complexe Hartsville pour les 50 prochaines années. Donc, ce que nous faisons, c’est de convertir la machine no 10 en une machine à carton recyclé à 100 %. Actuellement, il utilise 50/50 fibres de bois franc recyclées et vierges pour produire du milieu ondulé, ce qui est ce qui est utilisé dans les boîtes en carton.
L’URB de fabrication devra remplacer et ajouter de nouveaux actifs à la machine actuelle pour permettre la fabrication des grades de papier actuels pour nos essuie-mains légers et nos grades de papier aux grades de tube et de noyau plus lourds. Cette machine est conçue pour produire un large éventail de grades. Le projet Horizon intègre également un tout nouvel entrepôt de 109 000 pieds carrés qui abritera deux enrouleuses hors ligne pour couper le papier sortant de la machine no 10 .
Alors, comment êtes-vous devenu responsable de la gestion du projet Horizon?
Eh bien, en tant que directeur régional, le complexe Hartsville relève de mes responsabilités, mais j’ai également beaucoup d’expérience avec la machine à papier no 10 . La majeure partie de ma carrière a été consacrée à cette machine. Mes connaissances et mon expertise correspondent bien à l’attente que j’assumerais une partie du leadership de ce projet.
J’ai pu diviser mon équipe en deux groupes, dont la moitié se concentre sur le projet Horizon, dirigé par Jonathon Saleeby, et le reste gère les activités quotidiennes, dirigé par Jonathon Anderson. Donc, il a été difficile pour tout le monde d’assumer de nouvelles responsabilités. Fait intéressant, j’ai trouvé une citation de 1994 où nous avons d’abord étudié la mise à niveau de cette machine. J’ai toujours rêvé de passer au niveau supérieur, et je suis très enthousiaste à l’idée que cela se produise enfin.
Y a-t-il quelque chose qui vous a préparé à cette situation dans votre contexte?
Rien! Je veux dire, j’ai de l’expérience avec la machine n° 10 , mais rien ne m’a complètement préparé pour cela. Cela a été très difficile. Il faut une armée de personnes pour gérer un projet de cette taille. Avec un complexe de 100 ans et des machines de 70 ans, chaque fois que vous ramassez une boule de saleté, vous ne savez pas ce que vous pourriez découvrir. En fait, nous avons trouvé une bouteille de Coca-Cola qui était brune et dont la date était 1915 .
Comment relevez-vous les défis qui se présentent sur un projet aussi important?
C’est une approche d’équipe. Nous avons beaucoup de bonnes personnes impliquées. C’est beaucoup de réunions et beaucoup de « gestion du chaos », comme nous l’appelons, pour gérer ce qui se passe au quotidien. Les problèmes de livraison ont probablement été l’un de nos plus grands défis. C’était quelque chose que nous n’avions pas prévu. De plus, la météo a une incidence sur presque tout ce que nous faisons. Nous étions censés verser la première dalle de béton pour l’entrepôt la même semaine qu’un ouragan devait arriver. Nous avons dû trouver comment remonter le calendrier de quelques jours pour réduire l’impact des pluies abondantes possibles sur tout le travail effectué jusqu’à ce moment. Nous avons dû impliquer beaucoup de personnes pour essayer de tout garder sur la bonne voie.
Qu’est-ce que ce projet offre en termes d’améliorations de la durabilité?
We are converting from producing our product from 50% virgin hardwood fibers to 100% recycled fibers. Eliminating this virgin pulp mill definitely helps out from an environmental standpoint since we can eliminate the pulping operation as well as our chemical recovery operation. This leads to greenhouse gas reductions and fresh water reductions.
Nous essayons également d’être durables pendant le processus de construction réel. Nous recyclons beaucoup de béton et de matériaux de la démolition qui retournera dans la construction de la cour entrante.
Quel est l’impact communautaire du projet?
Le plus important, c’est que, comme je l’ai mentionné, la remise à neuf assurera que le complexe Hartsville maintient la station ici et est concurrentiel pour les 50 prochaines années. Il a plus de 100 ans maintenant, et il n’y a vraiment aucune raison que cela ne puisse pas durer plus de 100 ans.
Nous avons également essayé de nous concentrer autant que possible sur l’utilisation de fournisseurs et d’entrepreneurs locaux pour le projet.Depuis le début de l’ année, nous nous sommes engagés à dépenser 25 millions de dollars dans le comté de Darlington et 50 millions de dollars en Caroline du Sud au total. Nous avons rencontré des dirigeants municipaux, et ils nous ont dit que la capacité de l’hôtel était de 95 % avec tous les entrepreneurs que nous avons ici. Les restaurants sont également en plein essor. À une époque, nous avions jusqu’à 500 entrepreneurs sur place, et nous avons en moyenne environ 100 à 150 entrepreneurs par jour.
Qu’est-ce qui vous motive, vous et votre équipe?
Je suis très chanceux d’avoir un groupe solide de personnes qui travaillent avec moi sur ce projet. Nous comprenons tous son importance et son impact sur l’entreprise et la communauté. Personnellement, pour moi, la machine no 10 était l'endroit où j'ai commencé ma carrière chez Sonoco, et c'est là que j'ai appris comment les opérations fonctionnent et comment devenir un leader. Pour cette raison, j’ai beaucoup de responsabilité et de fierté à vouloir que cette opération passe au niveau supérieur.
Nous avons plusieurs générations de personnes et de familles qui ont travaillé dans la division du papier à Hartsville, et je veux voir cela continuer. Je viens d’une petite ville où mon père travaillait dans une usine de papier et son père l’a fait et ainsi de suite. Hartsville me rappelle beaucoup où j’ai grandi, et je veux que cette expérience générationnelle se poursuive. Mon équipe comprend l’impact de l’usine de papier sur la ville et la communauté. Ils connaissent l’importance de ce projet et savent qu’il est fait correctement pour avoir un impact positif sur l’avenir des individus, la communauté et l’environnement.